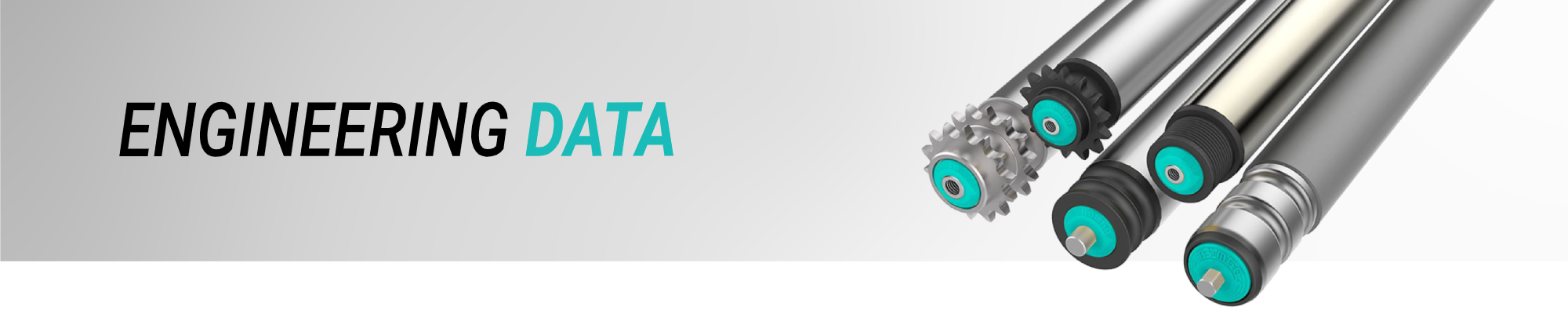
LOAD CAPACITY
- The tube, shaft, and bearing determine the roller load capacity. The load capacity (how much weight a roller can handle) is determined by the weakest of the three.
- The rated load capacity of a single roller is the uniformly distributed load on the roller surface (not point load).this is a list item
- The method of mounting the shaft to the conveyor frame impacts load capacity. For example, an internal threaded shaft has a higher load capacity than a loose-mounted shaft (e.g., a spring-loaded shaft).
- How flat is the product conveying surface? Are any partial forces encountered during conveying? This may affect load capacity.
- Steel tube and stainless steel tube are generally considered to have the same load capacity.
- A thicker tube may make the roller less likely to dent. It will have little influence on the roller's load capacity.
- In some modes of conveying, duty (the maximum load of a driven roller) may be more important than the load capacity (the roller's maximum weight capacity). The duty depends on the driving force (e.g., belt maximum tension, chain tension).
RUN OUT PERFORMANCE
- Run out is the key factor in how smoothly a roller runs.
- Excessive run out will lead to product jolting and deviation from normal conveying direction. It could also cause higher noise levels, partial product damage, or a reduction in the conveyor's lifespan.
TUBE MATERIALS
- Steel: daRollers are made from hot rolled seamless tube, resulting in better appearance, more balance, and less cost.
- Aluminum: Aluminum rollers are suitable for light-weight applications and wet working conditions
- Stainless Steel: Stainless steel is more durable and less prone to corrosion than common steel tubing.
TUBE SURFACE TREATMENTS
- Galvanized Coating: Galvanized coating provides multiple layers of protection against corrosion.
- Resistant to cracking and flaking of coating.
- 99.9% pure zinc applied finishing with a clear topcoat.
- PVC Sleeving: PVC sleeving combines most of the properties of rubber lagging. It has a short lead time and is cost effective.Material: Soft PVCTube Diameter: 1.9"Thickness: 2mmColor: Grey, RAL7037Hardness: Shore (A) 63 ± 5Resistance: No resistance to oil and gasolineElectrical Insulation: Non-conductingSuitable Temperature: –25°C ± 50°COther: Not food grade material
- Typically the sleeve covers the roller's outside surface.
- If you only require part of the roller to be covered, please confirm the length of the PVC sleeve and the position.
- Increase the length of the PVC elastic sleeve where running the roller generates axial force (e.g., axial movement or axial push).
- The side of the roller with a groove should not be covered with a sleeve.
- Polyurethane Sleeving: Polyurethane sleeving provides the ability to absorb impact, increase traction, and reduce system noise.Material: PolyurethaneTube Diameter: 1.9"Thickness: 1/8"Color: OrangeHardness: Shore (A) 83 ± 2
- Typically the sleeve covers the roller's outside surface.
- If you only require part of the roller to be covered, please confirm the length of the polyurethane sleeve and the position.
- The side of the roller with a groove should not be covered with a sleeve.
- Available in other sizes, colors and hardnesses.
SHAFT
- The shaft bears the total load on the roller; the shaft must sustain the total weight.daRoller's shafts are made from high quality carbon structural steel.
- Shaft Size
- Round shaft (mm)d: 1/4″
- Hexagonal shaft (mm)d: 5/16", 7/16", and 11/16"
- Surface TreatmentdaRoller's standard shaft surface treatment is anti-rust oil.
- Installation MethodThe roller installation method determines the complexity of roller assembly. Different installation methods also influence the roller's load capacity.daRoller can install shafts to meet your custom requirements.Spring Loaded
- Assembly and disassembly is simple and quick.
- Installation clearance is required between the inner width of the frame and the roller. Different clearances are required for different roller diameters, shaft diameters, and roller height. Typically allow 0.5 to 1 mm gap each side.
- Cross braces are required between the frames to stabilize and reinforce the conveyor.
- Spring loaded shafts are not recommended for sprocket rollers.
Internal Thread- This is the typical installation method for sprocket rollers. The roller is fastened to the frame with a bolt on each end.
- Assembly and disassembly is more time consuming.
- Bolt hold clearance in the frame should not be too large. Typically the clearance should be 0.5 mm. For example, an M8 bolt requires an Φ 8.5mm.
- When using an aluminum frame, use a large diameter shaft with a small diameter fixing bolt to reduce the risk of the shaft breaking through the aluminum frame.
BEARINGS
- The bearings are the most important component of the roller. The correct choice of bearing directly determines the reliability and lifespan of a roller. daRoller is the exclusive distributor and licensee of Damon bearings.
OTHER DESIGN CONSIDERATIONS
- The longer and wider the product, the more likely the products will convey in a straight line. If the products are very short and small, consider installing auxiliary devices to ensure the products convey straight.*
- The taller the products, the higher the risk of them falling over during conveying. Consider the following solutions:
- Reduce the roller pitch to allow more rollers to support the products.
- Avoid sudden acceleration or braking.
- When conveying on an incline or decline, check the center of gravity of the products to determine the risk of the products falling off the conveyor.
- daRoller’s antistatic design inside the roller will transmit the electric charge to the roller shaft and will discharge it through the earth connection (ground) to the conveyor frame. Do not allow the frame surface treatment to inhibit the ground.
- The conveyors described are for non-impact loading. Where impact loading occurs, reinforce not only the conveyor frame and support legs but also the roller.
- Reduce the roller pitch accordingly.
- Increase the roller diameter or tube thickness.
- daRoller’s standard products will satisfy your operational requirements under normal environmental conditions and humidity. If the rollers are subject to long-term exposure in a humid environment, please consider stainless steel or other waterproof and anticorrosive materials.